建材事業部、主任のうっちゃんです。今回の「さんずんごぶ」のお話は・・・
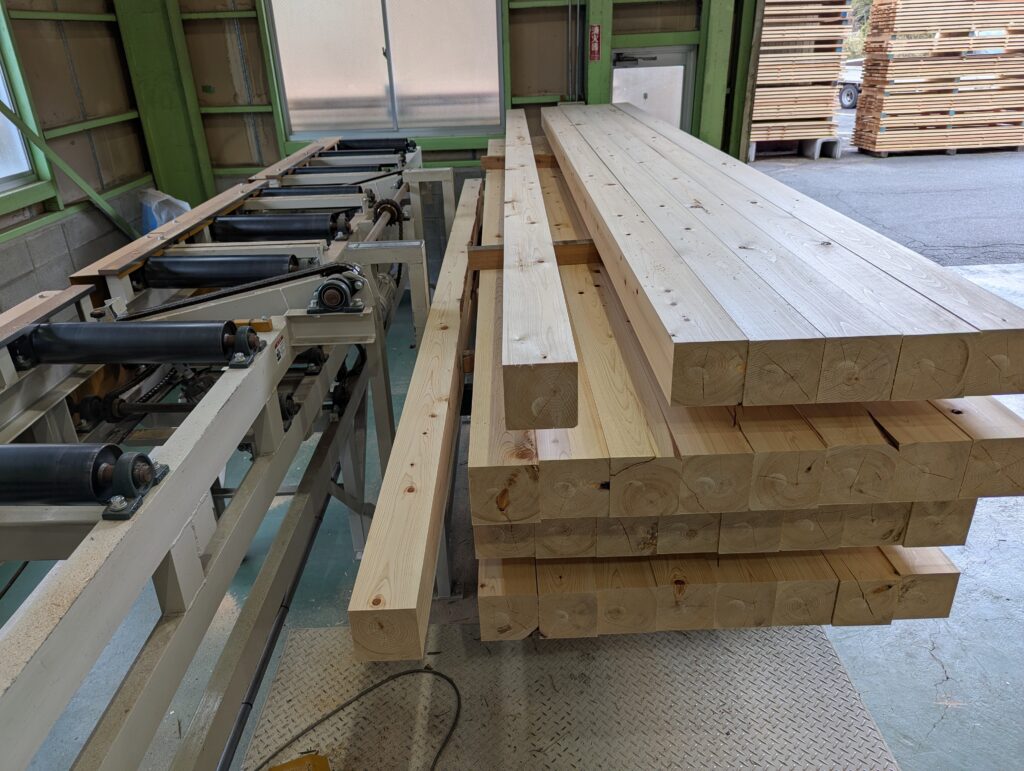
今回は製材工場にあるモルダー及び関連機械を使用し、しそうの森の木では主に土台に使用するヒノキ材の3寸5分角「さんずんごぶかく」を削る作業です。私たちは「さんずんごぶかく」を、略して「さんごかく」と呼ぶことが多いです。
このヒノキの3.5寸角「さんごかく」は、ここで削った後プレカット工場に移動し、大工さんの手によって墨付け、仕口加工を経て土台として新たな人生 (木だから木生か)を歩む事となります。
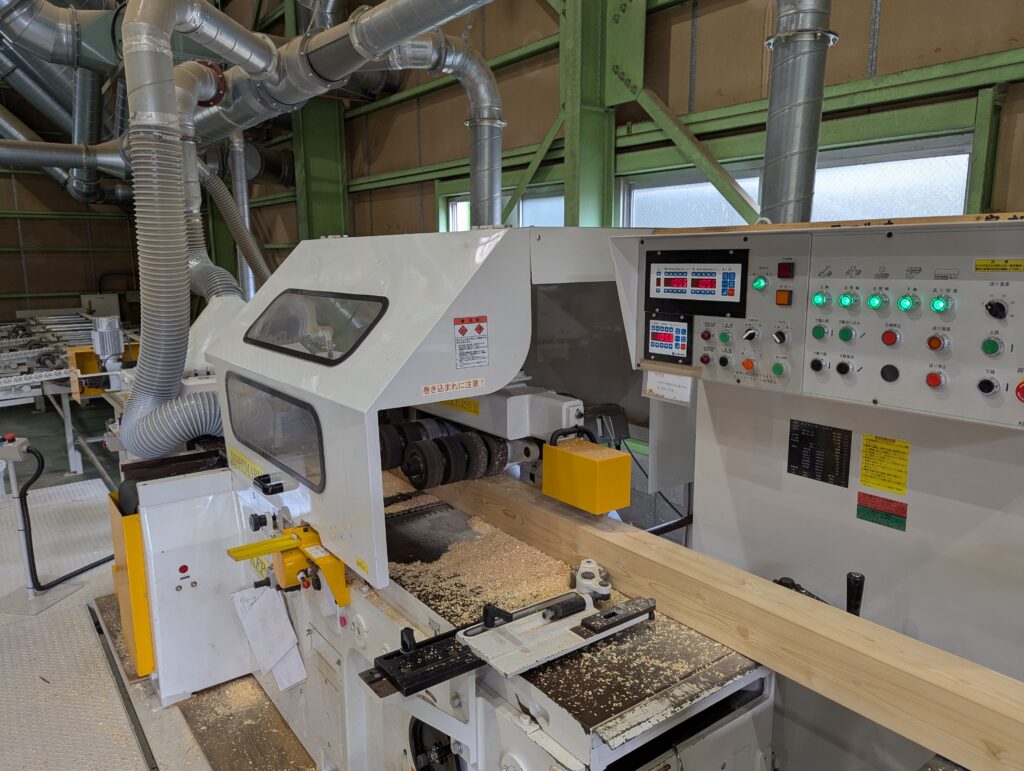
製材工場のモルダーはとってもコンパクト。本体より操作盤スイッチパネルの方が大きいような気も。
今回削っている「さんごかく」のヒノキ材はこの後、大工さんのところに運ばれるわけですから、曲がっているだの、割れているだの、使いにくいだのと文句を言わせてはいけません。より真っすぐに、より美しく、より使いやすく、を目指して削ります。・・・まあ、あくまでそういうイメージでという話ですが。
では具体的にどう削ると大工さんの使いやすい材になるの?と、いう疑問が出てきます。これについてはモルダー加工をされる事業所や、担当者によって少しずつ違う、ヒミツ☆のコツがあるものなのです。
私の場合は、まず製材された材(表面が荒いことから転じてラフ材という)の4面をよく観察し、その材がまだ山に生えていた頃、どのように生えていたのか、これを考えます。東西南北どの向きに生えていたか、その山では普段の風向きはどちらなのか、どのくらいの密度で植林され間伐されたのか、山の斜面は急だったのか緩やかだったのか・・・。こういった情報が、実は木材からある程度、うかがい知る事ができるのです。特に曲がり方や、木目の模様、年輪の間隔、木の色、密度、節の形状などから判断するのですが、もちろん、そんなに簡単ではありません。
これらの情報をもとに、「さんごかく」のヒノキ材を削るのですが、木材なので当然断面は4角形、つまり削る面が4面あるわけです。その4面を削る際に重要なのは①上面を何ミリ削るか。②下面を何ミリ削るか。③左面を何ミリ削るか。④右面を何ミリ削るか。当たり前のようですが、これを決めるのが何より肝心なのです。私の場合は、例えば削る本数が100本あるとすれば、大まかに3パターンぐらいに仕分けをします。もし100本を100通りのパターンで削ろうものならいくら時間があっても作業が終わらず、帰ってビールを片手にナイターを観ることなど夢のまた夢になってしまいますからね。大まかに3パターンに分けます。そして、削る前後で答え合わせをしながら、仕上がりを確認していきます。「さんごかく」の木の声を聞きながら。
この様に、モルダーの機械では、単に寸法通りに削れれば良い、というわけではなく実は非常に多くのことを考えながら作業しています。今こうして整理しながら書いていても、気を付ける点などが多すぎてまだまだ書ききれず、我ながらなんと難しい仕事をしている事か、とも思います。
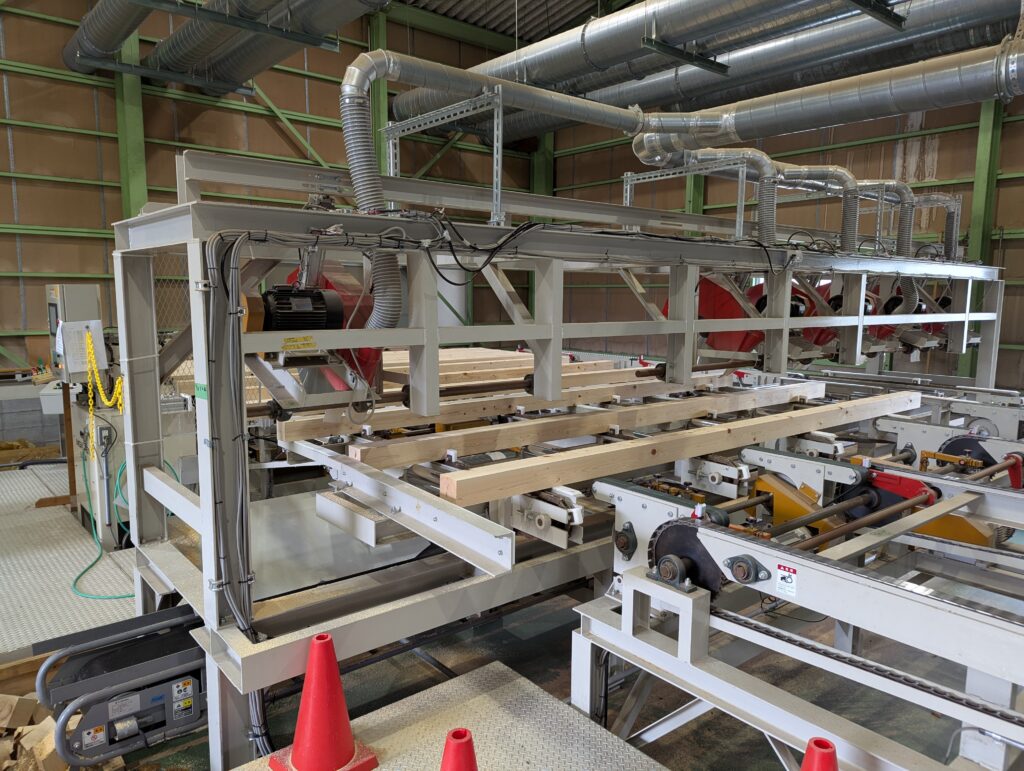
モルダーでピッタリ3寸5分「さんずんごぶ」つまり105mmに削った後は、やや大がかりな「自動長さカットマシーン」的なセクションを通り長さを切りそろえます。直径60センチの大きな丸ノコが並びます。3m~6mまで対応可。
山から製材工場へ丸太が運ばれて来る段階では、まだ長さは切りそろえられておらず、理想より少し長かったり短かったり、いろいろです。山では重機であったり大きなチェーンソーでズババババーン!といかにも荒々しく伐採するので、長さの精度など良くなくて当たり前です。
なので、モルダー後に長さを切りそろえると、「さんごかく」も引き締まった男前に見えます。
これなら、今回モルダー加工した「さんごかく」を無事、世に送り出し、工事をして頂く大工さんにも、施工主のお客様にも喜んでもらえるかな。
それでは、また。